|
HOME
Drum Mix Plant {DM–35 (30/40 TPH), DM–45 (40/60 TPH),
DM–50 (60/90 TPH),
DM–60 (90/120 TPH), DM–65 (150 TPH
) } |
|
Vishvakarma
is the plant of choice for contractors all
over the india, who demand affordable
large-scale production, long-terms
performance and lowest operating costs per
tones of asphalt. Plant focused on
delivering a simple, dependable easy-to
operate and maintain. Truly plant with a
durable design that lets contactors be
competitive on both large and small
projects.
|
|
|
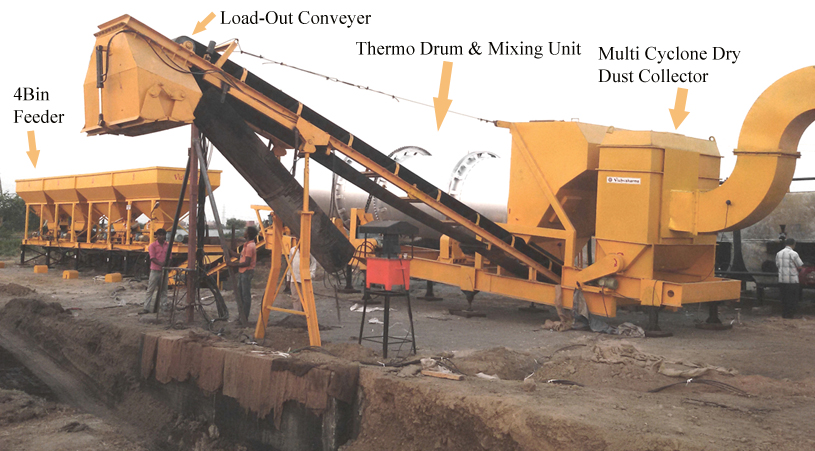 |
|
Four bin feeder unit
is having four bins and each bin is driven by individual DC motor drive so as to accurately conveyor, flow of aggregate from each bin.
Vibrating arrangement of bin, low level & no
flow warning device of bins. four bin feeds aggregate to gathering conveyor which is driven by motor drive. it is fitted with electronic weighting system material is form gathering conveyer flow to vibrating screen for removing over size material. |
|
|
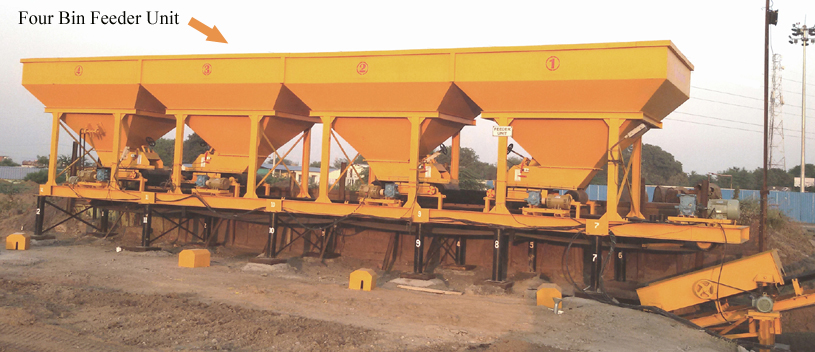 |
|
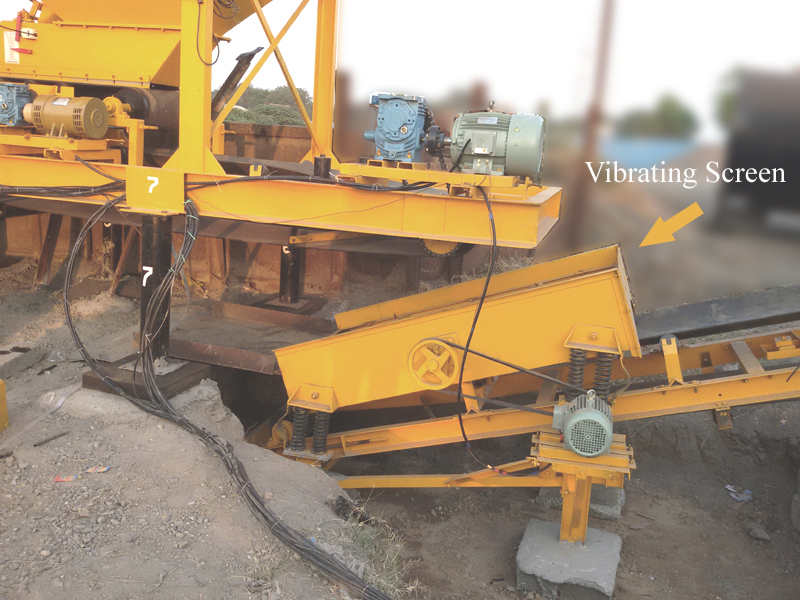 |
Vibrating screen
removes oversize materials and feeds the remaining
materials to charging conveyer. Separate size of screen can be provided for removing oversize material is form different kind of mix.
|
Slinger conveyer
is provide for transferring the aggregates received from gathering conveyer as well as from vibrating screen after removing the oversize aggregates and discharging, it into dryer drum under combustion zone. |
|
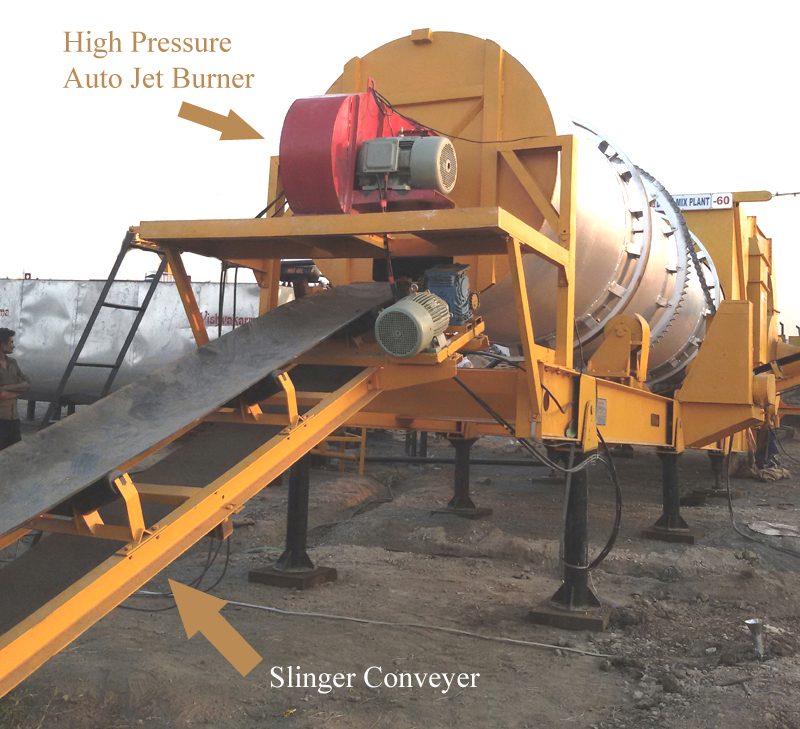 |
|
|
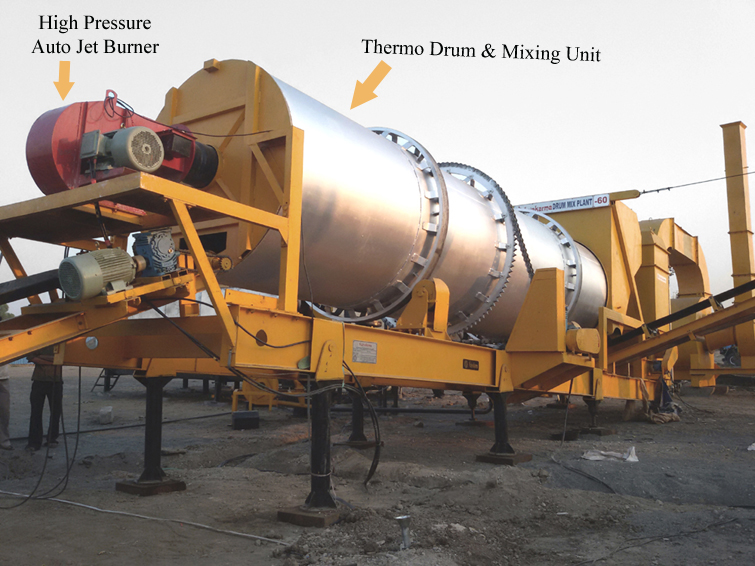 |
|
|
Thermo-drum & mixing unit
of the drum mix
asphalt plant is the heart of the plant. As
called the aggregate is headed with
automatic burner to require
temperature and bitumen is added in the
drum at suitable stage and bitumen is coated
evenly to the aggregate in this drum. There
are various stages in the drum like heating
, mixing zone. That helps the aggregate and
bitumen to heat and mix uniformly. The fins
in the dryer unit are specially designed to
get maximum heat efficiency that is to say
minimum heat loss.
Dust collector unit
is fitted
at the rear end of the plant, that is at the
out put end of the plant. It is having an
efficient dust collecting system and fitted
with shutter, with can be varied as
required. An exhaust fan having sufficient
capacity to ensure an effective airflow
through the dryer and through the dust –
collecting unit.
Exhaust
fan having sufficient
capacity to ensure an effective airflow
through the dryer and through the dust
collecting unit.
Load-out Conveyer
is elevates
the mix aggregate to such height that
the mix material can be directly loaded in
the dumper . it is fitted with hydraulically
operated hopper whit helps the material to
fall without segregation
|
|
|
|
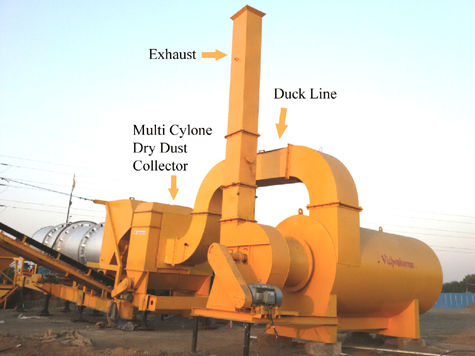 |
Pollution Control
Unit (Extreme
Turbulence Venturi
Type) |
|
Exhaust inducts hot
gases from the
thermo drum unit,
Higher pressure
water jit is sprayed
on to the gases
which forms water
based slurry and
deverted to the
sludge pond. Air
pressure is reduced
and remainting gases
are exhausted. The
pond is made such
that, the surface
water is again
reused. |
|
Nozzles and
water bearing plates are made of stainless steel to resist corrosion. The
sludge pond requires to be cleaned once a week based on normal site conditions. As a safety measure, always surround / cover the
sludge pond with wire fence sonce, working temperature of water may be above 80
degree. It is also necessary to have the drain pipe submerged in pond.
|
|
|
Bitumen Tank
an insulated storage tank is designed with heating system. It is insulated to prevent heat losses. Tank is equipped with separate automatic electric burner for heating the asphalt. Automatic burner makes a hot gas stream through pipe for heating. 25 mm thick external insulated with steel sheet covering. Temp-Gauge is provided for examining the status leading to uniform quality. It is fabricated by using M.S. Section and plates. It is having 10, 15 upto 30 Tones capacity in various safe like round and U safe. |
|
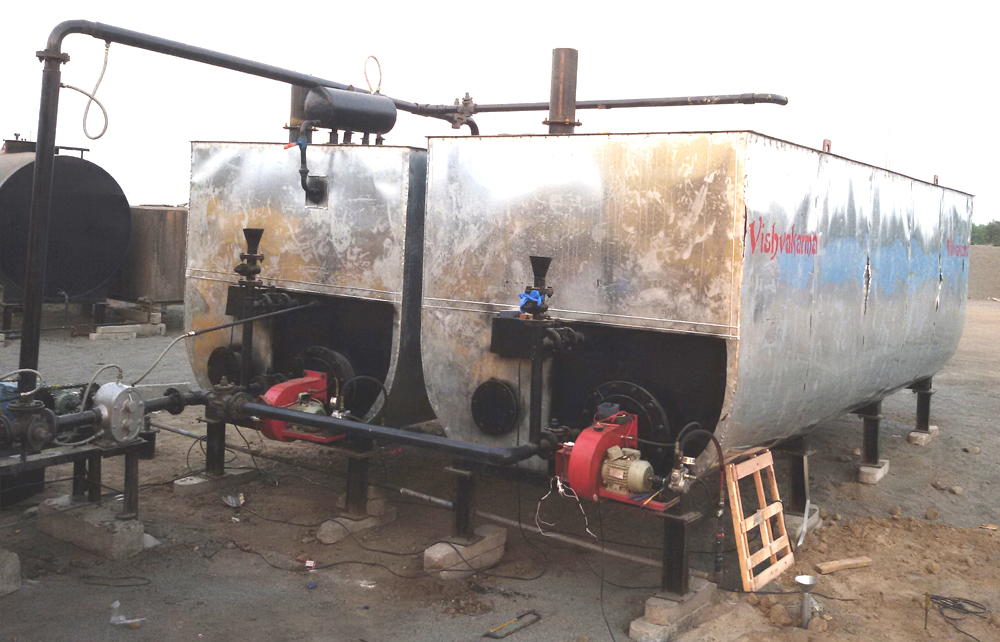 |
|
|
|
|
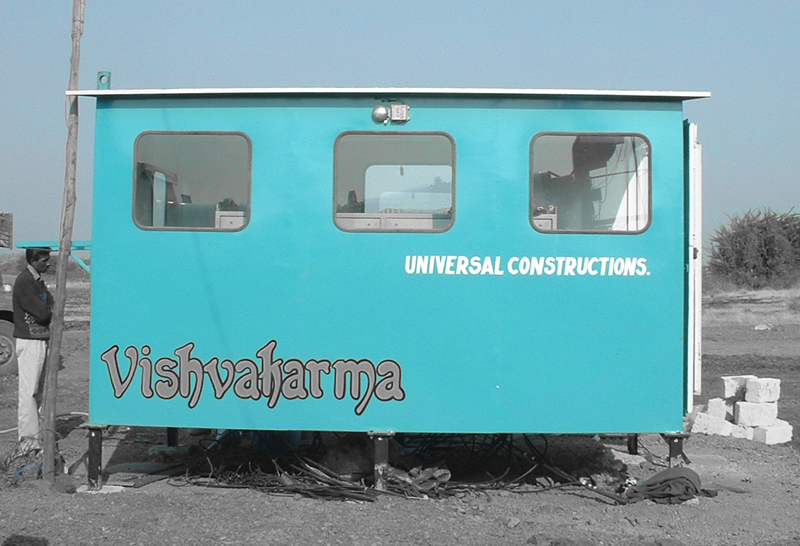 |
Control Cabine
is insulated cabin is provided with electric panel to operate the entire plant , the cabin may not have air conditioning system as per client requirements.
|
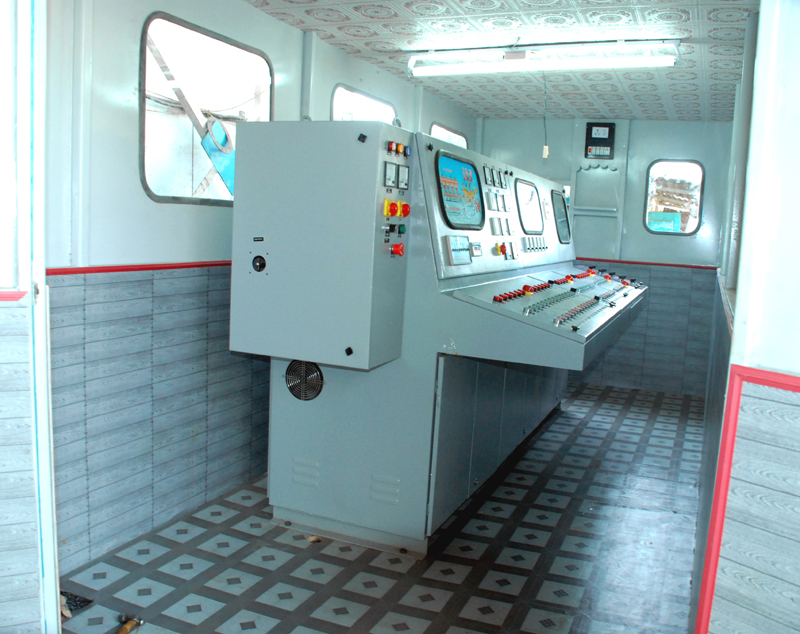 |
Electric control panel
is fabricated from 16 SWG CRC sheet and processed with painting, the panel has in –feed master control, Aggregate flow measurement system, which controls asphalt flow, individual bin, asphalt flow indicator, automatic synchronization of aggregate with
asphalt, aggregate and asphalt with totalizer
printer for print -out record of all parameters for
an instant verify of formula, automatic temp
controls with indication, metering for aggregate,
asphalt, input voltage, moisture and motor load. |
|
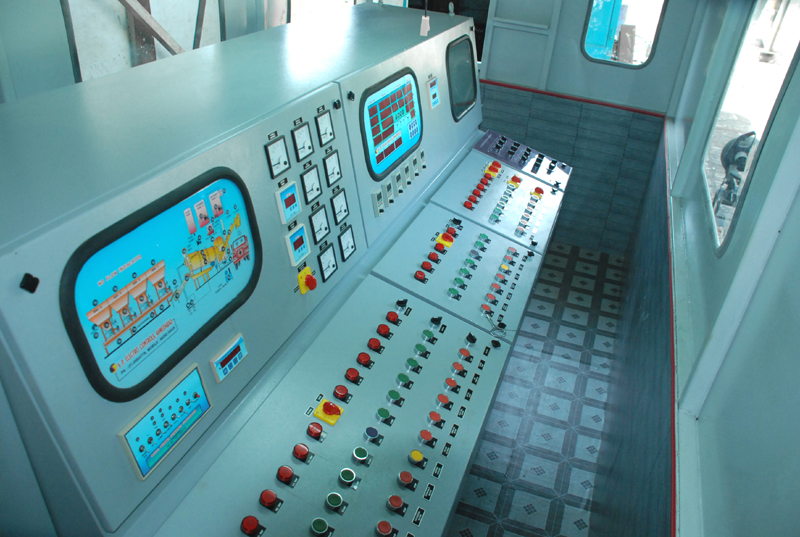 |
|
|
|
|
|
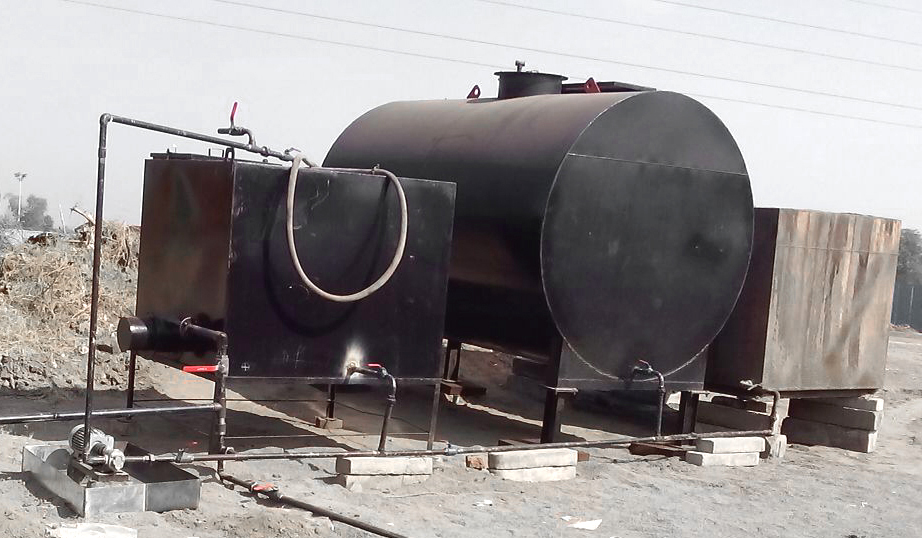 |
Fuel tank
is also supplied with the plant, having
10000 lts capacity with 2000 lts service
tank.
Mineral / Lime feeler unit
is also fitted at the output end of the
plant, this unit into lime / cement /dust
feeding rotary pump with fitted motor drive
and air blower quantity of filler material
to be added in the mix. |
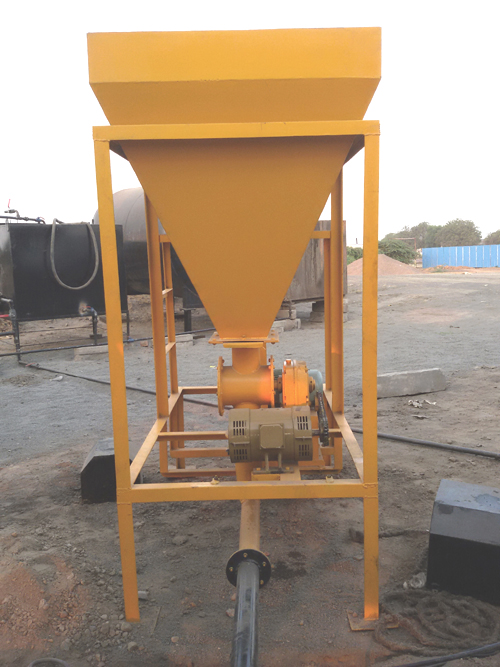 |
|
|
|
|
|
|
|
|
|
|